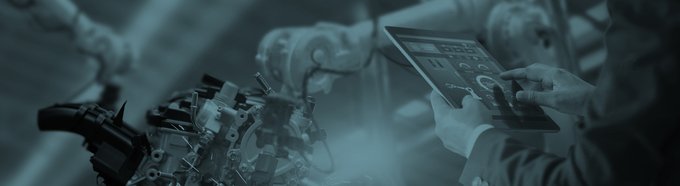
Digital Factory
The driving force behind your factory’s digital transformation.
Smart virtualization and networking of your production processes, efficient use of your equipment and production resources for sustainable results – there are a multitude of reasons why you might decide to digitally transform your production systems. How can you achieve this without taking any risk? With 30 years of cutting-edge experience in automation technology and plant engineering, we'll be there to support you with exploiting the full potential of the digital factory for your production. From (3D) simulation to virtual commissioning and the digital twin – we’ll take your plant projects to a new level, together.
Our services
- We’re able to advise, design and implement 3D simulations, as well as virtual commissioning for your automation projects, without being dependent on software – no matter what industry you’re in:
– Simulations of production plants (plant engineering, conveyor technology) & special machines (e.g. to safeguard throughput assumptions or cycle times).
– Creating virtual models of intralogistics and production plants (e.g. for virtual commissioning, for training purposes, etc.)
– Creation of behavioral models (e.g. SEW, Siemens drives, RFID readers, etc.)
– Implementation and support of virtual commissioning with SiL and HiL (software/hardware in the loop)
- We are constantly working on building our virtual models more efficiently so you can use them during your plants’ entire life-cycle – as a digital twin, tailored to your use case that gives you just the right support you need, when you need it e.g. for remote servicing, and during ongoing operations.
Your benefits
- Achieving greater efficiency and saving time & money at all levels of your production processes.
- Detecting conceptual errors in your plant layout at earlier stages, and eliminating them in a more cost-effective way by carrying out the engineering disciplines for your plant projects at the same time: hardware/electrical design, software development and commissioning.
- Improving quality: Minimize the risk of malfunctions, failures or unplanned shutdowns by systematically testing coverage on the virtual plant.
- Unleashing the potential of the digital factory, far beyond commissioning – with the virtual plant as a digital twin in operation:
– Safe training on the digital model
– Testing risk-free extensions/adaptations of the plants prior to commissioning actually taking place
– Efficient remote service using AR (augmented reality)
References
Battery assembly | SiL with F.EE Screen, 6 lines, 32 PLC, 35 robots |
Intralogistics warehouse | SiL with F.EE Screen, 14 PLC, 7 robots, high bay warehouse with 12.000 bays |
Conveyor system | SiL with F.EE Screen, 500 conveyors, 2 PLC |
Heavy-duty overhead conveyor (s7 classic & TIA) | WinMod + SimLine |
Car and worker bell | WinMod + SimLine |
High-bay warehouse (6 plc TIA connected) | WinMod + SimLine |
Skid conveyor technology | WinMod + SimLine |
Several body and white projects (TIA, S7 classic) | EKS Suite |
Several body and white projects (TIA) | Process Simulate, BMW SAS |
Assembly/Battery production lines | WinMod + Process Simulate |
Conveyor technology | Plant Simulation |
Battery modul / pack assembly line /feasibility studies | Plant Simulation |
Skid conveyor technology (conveyor technology with buffer) x-plcs | EKS Suite |
Body in white / assembly | WinMod + Process Simulate |
Battery assembly lines | WinMod + SimLine + Fanuc RG |
Special machinery | Process Simulate |
Digital Factory