Process control system 800xA: High performance for our customers.
Task: | merging a number of independent projects into the process control system ABB 800xA with „High Performance HMI“ | |
Department: | EMSR/PLT | Process | |
Business: | chemical industry |
Our customer is one of Germany's leading chemical companies. In the year 2012 they trusted VESCON with transferring four ABB Freelance 2000 projects into the new process control system ABB 800xA with „High-Performance-HMI“. The task assigned to VESCON was to coordinate the interfaces in close cooperation with LANXESS and ABB and to create new control diagrams in the process control system 800xA:
- 3 graphic images level 1
- 25 graphic images level 2
- 120 graphic images level 3
Services provided by VESCON:
- coordination
- projecting of the process control system ABB 800xA
- FAT / SAT control diagrams
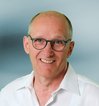
Salt transport on our customer's premises.
Task: | installation of a pneumatic conveyor unit to replace an existing belt conveyor | |
Department: | process engineering | process | |
Business: | chemical industry |
The fine salts occurring after a drying process used to be mechanically transported via a belt conveyor system into a fine salt bunker.
These salts were supposed to be optionally integrable into the coarse salt system running in parallel. In view of the long conveying distance a pneumatic conveyor system was installed for the transport. The separation of the conveyed material at the top of the bunker took place via a cyclone separator. Apart from that it was ensured that the conveying air could be integrated into the existing waste gas purification system.
Services provided by VESCON:
present-state analysis
- accompanying tests on site regarding the service life behaviour of the product mixture
- projecting and design of the pneumatic conveyor system and the cyclone separator
- checking and adjustment of the existing gas purification system
- creation of the technical sheets for all components to be supplied or modified
- layout and pipeline planning for different variants
- checking the incoming documents of the component and unit suppliers
- accompanying assembly monitoring
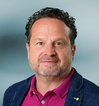
Division Head Plant Engineering Process
Phone +49 6233 6000-580
thomas.gaertner@vescon.com
Salt drying on our customer's premises.
Task: | installation of a new drying unit to increase production | |
Department: | process engineering | process | |
Business: | chemical industry |
In the course of a production process saline solutions occur which used to be dried for further use by being passed through several pre-drying stations of a rotating drum system.
In order to increase the throughput of the plant the rotating drum system was to be replaced by a fluid bed drying system having a three times higher throughput capacity.
The new system was supposed to be put up at the same place as the old one, so that the old unit had to be dismantled and removed first. These works were carried out during an intermediate revision phase which was tightly scheduled. The cramped conditions on site represented an additional challenge. The necessary peripheral logistics such as the product feed and discharge, the dryer air supply and venting as well as the cleaning, energies like steam pressure, compressed air etc. had to be adjusted accordingly to the higher demands.
Services provided by VESCON:
- present-state analysis
- process simulation of the new requirements for assessment of the peripheral measures
- projecting and design of the new machines, devices and units
- creation of the technical sheets for all new components to be acquired
- development of a dismantling and assembly concept
- layout planning
- scheduling
- checking the incoming documents of the component and unit suppliers
- accompanying assembly monitoring
- accompanying start-up including implementation of process optimization measures
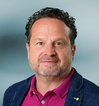
Division Head Plant Engineering Process
Phone +49 6233 6000-580
thomas.gaertner@vescon.com
Sulphuric acid plant on our customer's premises.
Task: | increase of the conversion performance of a wet catalytic sulphuric acid plant | |
Department: | process engineering | process | |
Business: | chemical industry |
In a wet catalytic operation for producing sulphuric acid after a metallurgical process the conversion rate was supposed to be raised to such an extent that compliance with the demanded emission values for sulphuric acid was guaranteed. VESCON accomplished this goal by increasing the number of conversion stages through the installation of an additional converter unit, with the existing plant components and processes being maintained as far as possible. The integration of the new unit took place parallel to the existing one, with only a short time being allowed for the switch-over.
Services provided by VESCON:
- present-state analysis
- evaluation of the existing process data
- process simulation of the present state
- process simulations of various approaches in the planning phase
- discussion of simulation results with the plant operator
- working out details of the preferred solution (mass and energy balances, creation of flow charts, process and functional descriptions etc.)
- support in realization and start-up
- creation of the operation manual and the final documentation
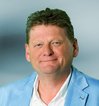
Batch house and tank control system for our customer.
Task: | reconstruction of a production plant, project planning and project management | |
Department: | EMSR/PLT | Process | |
Business: | chemical industry |
Our customer is one of Germany's leading companies when it comes to automation technology. Since 2006 VESCON has been supporting this customer in the field of process automation by providing services related to project planning and commissioning. In the above mentioned project VESCON has handled the complete detailed engineering for the following services:
- Projecting of a completely new process control system "ABB Freelance 2000“ including:
- tank control / regulation
- 2 pieces ABB AC800F, redundant
- Profibus coupling with 5 pieces ABB S900, approx. 500 I/O
- Modbus coupling to E-filtration plant with approx. 150 I/O
Projecting of the batch house control system with 4 operator stations and OPC coupling to the higher-level raw materials management system with formulation transfer to the PLS:
- 3 pieces ABB AC800F
- Profibus coupling to 6 pieces ABB S500, approx. 600 I/O
- Profibus coupling to S5 100U via CP543 approx. 200 I/O
- Profibus coupling to ET coupling to 200, approx. 200 I/O
- Profibus coupling to HM coupling to S Fieldbus Systems AB
- Profibus coupling to Schreurich and Ramsey Waagenterminals (weighing terminals)
- Services provided by VESCON:
- project planning
- simulation programme
- FAT / SAT
- project management
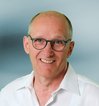
Know-how is the best medicine.
Task: | construction of a new kilo laboratory | |
Department: | EMSR/PLT | Process | |
Business: | chemical industry |
Our customer is one of Germany's leading pharmaceutical companies. VESCON received the order to plan, automate and commission a kilo laboratory at the company's Berlin location. Within this project VESCON has provided the entire detailed engineering for the following services:
Hardware engineering for
- 2 agitator reactors (30l, 60l) by Büchiglas
- 5 autoclaves by Premex
- vacuum system including 2 compressors
- secondary facilities
Software engineering of the process control system Siemens PCS7 including
- 1 piece Siemens S7 417
- 2 operator stations
- 2 additional operator terminals MT316 Ex by Stahl around the reactors
- 160 PCS stations, approx. 560 data points in 2 data collectors, Profibus ET200
- 7 converters
- approx. 40 control loops, 5 of these flow controllers by Bronkhorst for pressure regulations up to 300 bar
- 2 cryostats by Huber
- step sequences, formulas
Services provided by VESCON:
- E-MSR hardware design with EPLAN
- switch gear cabinet construction (sub-supplier), delivery and assembly
- E-MSR assembly on site
- projecting and supply of the process control system Siemens PCS7
- simulation programme
- FAT / SAT / cold commissioning
- project management
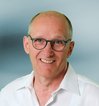
The essence of a successful cooperation.
Task: | construction of a distillation plant with glass reactor | |
Department: | EMSR/PLT | Process | |
Business: | chemical industry |
Our customer is a leading manufacturer of glass reactors/laboratory technology. In 2011 this company and VESCON cooperated in a process automation project constructing a glass reactor as a test plant located in an area with potentially explosive atmosphere on a customer's premises. VESCON was responsible for the detailed engineering of hard and software:
Projecting a panel PC with the visualization system „WinCC Flexible 2008“
Plant control / regulation:
- power and control cabinets
- 1 piece Siemens S7 315 CPU
- Huber temperature control system
- 1 Stahl Touch Panel PC with Windows CE and WinCC Flexible (Ex)
- control and overview diagrams of the plant
- alarm display
- trend displays
- user management
Services provided by VESCON:
- E-MSR hardware planning with EPLAN
- switch gear cabinet construction (sub-supplier), delivery and assembly
- projecting and supply of the control system and the operating panel
- FAT / SAT / cold commissioning
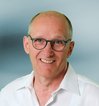
The stuff that success is made of.
Task: | construction of a grinding plant for the treatment of silicon carbide | |
Department: | EMSR/PLT | Process | |
Business: | chemical industry |
Our customer is one of the leading manufacturers of silicon carbide. As a long-term partner VESCON had already been trusted before with the projecting and commissioning of plants in quite a number of projects related to process automation. In the project mentioned above VESCON handled the entire software engineering for the following services:
- projecting of the control system with Siemens Step7
- 1 piece Siemens 315-2PN/DP CPU
- Profibus coupling to 3 pieces Siemens ET200M, approx. 400 I/
Scales connection to Siwarex with:
- projecting of the process control system "VISPRO“ including plant control / regulation
- control and overview diagrams of the plant
- alarm display
- trend display
- with one operator station on site
Services provided by VESCON:
- projecting
- simulation programme
- FAT / SAT / cold commissioning
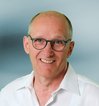
Step by step towards success
Task: | analysis and new creation of a fully automated start-up step sequencer of a chemical production plant | |
Department: | EMSR/PLT | Process | |
Business: | chemical industry |
In this plant our customer, one of Germany's leading chemical company, produces a basic chemical product which occurs after heating with a burner control system at a temperature of approx. 300°C and at an operating pressure of approx. 270 bar in a resulting exothermic reaction.
VESCON analysed the automatic start-up and shut-down system of this production plant and created a new step sequencer with start-up, various stop and shut-down programmes. Depending on the stop condition the sequencer can switch back to the different start-up parts or into the switch-off programme.
VESCON had been assigned the task to reprogram and simulate the individual parts of the programme. After a standstill of the plant the new start-up step sequencer was put into operation within a very short time.
The start-up step sequencer includes:
- approx. 150 steps
- 5 start-up parts
- 4 stop programmes
- 1 shut-down programme with various entries
Services provided by VESCON:
- coordination
- projecting of the process control system ABB Freelance 2000
- simulation
- FAT / SAT, cold commissioning
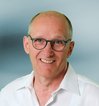