Successful conversion of a vehicle assembly with electric monorail system
Task: | Conversion and extension of a vehicle assembly with electric monorail system | |
Department: | Automation | |
Business: | Automotive |
The projekt:
A German automobile manufacturer commissioned VESCON Automation with the conversion of an existing final assembly line for passenger cars as well as the extension of the load capacity in order to be able to manufacture further vehicle types in the future. The conversion involved these three areas:
1. heavy-duty EMS with upstream conveyor belt
2. assembly crosshead final assembly
3. crosshead return transport
A project with many challenges:
- Highly demanding project in terms of technology and deadlines.
- Tight time frame for commissioning in order not to hold up the production process for too long
- Integration of the final assembly of a new vehicle type (e-mobility) into an existing plant
- Due to the ongoing production process, the assembly took place at a different location
- Limited space
Another challenge: the project was implemented during the height of the Corona pandemic and related Corona requirements affected implementation.
Overall, the project spanned a period of over three years.
Our implementation:
Virtual commissioning:
The existing plant was first converted into a virtual model. Specifically, the hardware and the entire PLC programming were imported. Everything was then simulated with the WinMOD software, which shortened development times, eliminated sources of error in good time and minimised commissioning costs.
Hardware design:
At the beginning, the designers familiarised themselves with the complete system. In particular with the power rail bus system, which establishes the connection between the head control and the trolleys. The entire communication of the system runs via this system. The position of each individual vehicle is identified at all times. Through numerous monitors along the line, the exact location of the vehicle can be called up and the feeding of components such as bumpers can be organised.
- Construction of a commissioning line
- Equipment of the running gear
- Planning of the additional EMS cycles into the existing plant
- Replacement of the feed cabinets
- Reconstruction phase
- Commissioning of the plant and support with peripheral tests
PLC programming & commissioning:
In terms of software, this was probably the biggest project ever for VESCON Automation. Programming with the existing software presented the following challenges:
- Only one employee could effectively work on each PLC at a time, which made it difficult to distribute tasks as well as progress over time.
- Converting an existing plant always means familiarising oneself with existing software programming, which was originally built by another manufacturer.
After reviewing the existing software, a model was developed for the VIBN to test the feasibility of the project in advance. In the next step, the plant software had to be adapted for the conversion and the hardware converted. After the conversion phase, the start-up and shift support began, as well as the follow-up and ongoing optimisations until the final acceptance by the customer.
Conclusion:
An existing plant was converted in such a way that it is now fit and running robustly for the next few years. The plant ran so stably in the first two days after the extension that all production targets were exceeded.
Precise and efficient: With VESCON to automated cable assembly.
Task: | Realisation of an automated cable assembly system for generator cables | |
Department: | Assembling | Automation Technology | |
Business: | Automotive |
For a leading supplier of energy and data transmission in the automotive and industrial sectors, VESCON Systemtechnik implemented an automated assembly line for cable harnessing.
The system offers the advantage that diesel as well as petrol variants can be processed and tested on an area of just 24 x 8.5 m - within a product-specific cycle time of 16-25 seconds. By linking the innovative assembly process with the production of matching workpiece carriers by means of 3D printing, VESCON Systemtechnik ensures a consistently high quality of the final products and avoids the problems that non-rigid lack cable harnesses can entail due to unwanted deformation. To ensure an ideal assembly, our experts also rely on automated camera testing based on the principles of machine learning (subfield AI).
Services provided by VESCON:
- Introduction of a new assembly concept
- Software engineering PLC
- Construction & assembly
- Commissioning
- Service & Training
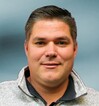
Department Head Sales & Distribution
Phone +43 3112 36006-750
christoph.legat@vescon.com
Move more with VESCON: KW-Kranwerke AG.
Task: | support in hardware construction, project planning and project management | |
Department: | Electrical engineering / Automation | |
Business: | machinery and plant engineering |
VESCON has been supporting the KW-Kranwerke AG in the fields of hardware construction, project planning and project management since the beginning of 2008.
The KW-Kranwerke AG continues the tradition of the Mannheimer Kranbau (Mannheim crane construction) and is an innovative medium-sized company that offers customized solutions and services. They focus on the supply of grab bridge cranes, gravel excavators, gantry and slewing cranes and specific hoisting solutions. In the German-speaking regions the KW-Kranwerke AG is the market leader when it comes to fully automated grab bridge cranes for waste icineration plants.
The cooperation with VESCON is characterized by openness and a spirit of partnership. Both companies assist each other in the development of new business fields and the search for qualified personnel.
Services provided by VESCON:
- project planning
- electro-technical engineering
- project management
- hardware construction
- EPLAN support
BMW - Roller control system Dingolfing
Task: | Roller test bench, development EPLAN, S7, Visu | |
Department: | Automation | |
Business: | Automotive industry |
- Roller test bench
- development EPLAN, S7, Visu
BMW - Chassis test bench USA
Task: | Chassis test bench, roller test bench, development EPLAN, S7, Visu | |
Department: | automotive | |
Business: | automotive industry |
- Chassis test bench
- roller test bench
- development EPLAN, S7, Visu
Porsche CMT welding plant for doors, PLC programming and commissioning.
Task: | PLC programming and commissioning, assistance and optimization | |
Department: | Electrical engineering | Automation | |
Business: | automobile industry |
Customer: IBS Dr. Klaus Schürer GmbH
In this project VESCON has realized the programming and visualization of the control system for a welding cell in the door manufacturing section.
The project implied the consideration of several interfaces and subsystems and the integration into an existing control architecture.
Systems and technologies used:
WinCC, Step7, SEW, ABB-Robots, Fronius welding control systems, safety technology
Services provided by VESCON:
- software engineering PLC including visualization
- interface programming
- risk assessment / Sistema analysis
- commissioning
- plant and cycle time optimization
- production support
- training and instruction
BMW - Roller Dingolfing
Task: | Rollenprüfstand, Entwicklung EPLAN, S7, Visu | |
Department: | Automatisierungstechnik | |
Business: | Automobilindustrie |
- Rollenprüfstand
- Entwicklung EPLAN
- S7
- Visu
See further with VESCON: Headlight assembly line for the new "eyes" of the BMW 7 model.
Task: | headlight assembly line | |
Department: | Special machinery engineering | Automation | |
Business: | automobile industry |
Drivers and owners of the new BMW 7 model enjoy state-of-the art light technology, not least owing to the assembly lines designed by VESCON. ZIZALA Lighting systems has developed a LED headlight and a unique "searchlight" for BMW which is produced in Austria. Thanks to our long-term experience in the field of light technology VESCON has been able to contribute to the successful production and high quality of the new "eyes".
As in the automotive industry the headlights have become a major design feature and are increasingly based on LED technology, the assembly processes are getting more and more complex and demanding. The result is that ever higher demands are placed on the plant constructors not only regarding control technology and ESD protection, but also with respect to the use of material having direct contact with the product during the assembly process and the total logistics operations around the plant. This implies the necessity for tracing batches and individual parts during the assembly process.
With more than 100 different components, such as boards, heat sinks, light bars, reflectors, and design trims, being involved and the assembly processes becoming increasingly complex due to this large number of parts, the headlight assembly line constructed by VESCON is the largest one ever used at ZIZALA.
The headlights are assembled and checked in line passing 15 partly or fully automated stations. The respective assembly processes like screwing, pressing or lasering run automatically. At the end of the assembly line the headlight is adjusted and the light pattern is tested automatically. After that the headlight is conveyed to the fully automated robot station where the adhesive bed is activated and the sealing and adhesive substance is applied by the robot. Then the pane is inserted and the completely assembled headlight is subject to a leak test. At the end, only 100 % tested headlights will leave the plant.
The newly developed "searchlights" that can be supplied on demand are also produced on a plant designed by VESCON. Thanks to an intelligent software and the on-board electronic system these headlights can identify obstacles at the roadside and illuminate them if they represent a potential source of danger. This assembly line as well has been produced at VESCON as a turnkey solution and then put into operation on the customer's premises.
Services provided by VESCON:
- concept development
- development and construction of a turnkey plant
- training courses
- production support
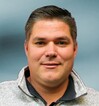
Department Head Sales & Distribution
Phone +43 3112 36006-750
christoph.legat@vescon.com
More power with VESCON: Turbo assembly line at BoschMahle Turbosystems.
Task: | turbo assembly line | |
Department: | special machinery engineering | Automation | |
Business: | automotive industry |
For economic reasons the downsizing of motors has become a decisive issue in the design of new automobiles and engines. As a consequence, the development focuses on the charging of ever smaller engines assigning a significant role to the use of turbo chargers.
For the Austrian production plant of BoschMahle Turbo-systems VESCON has designed and realized several plant concepts. This project included among other things the development and construction of an automatic picking machine which pre-assembles the small and delicate components supposed to be installed in a high-speed turbo charger in an assembly tray. These trays are then used in the fully automated assembly line. The individual components are stored in specifically designed revolving magazines and separated. This allows an uninterrupted production, as the individual cartridges can be reloaded from outside. The separated parts are placed in the tray via several axis systems. In addition, the data of all individual parts are read in via data matrix codes during the assembling process which guarantees the consistent tracing of the components.
In another plant developed by VESCON, where the pre-assembled trays are also employed, special chargers and turbo chargers for utility vehicles are produced in small quantities. As also for these chargers the same standards concerning quality and data tracking are demanded, we had to focus intensely on the measurement system capability and the process safety considering at the same time a higher degree of manual operations. In some sections manual operations alternate with fully automated processes. This coupling could be realized in a concept which had already been implemented several times before. Here, as well, all pressing, screwing and testing operations are recorded and the individual parts are conveyed to the plant while being batchwise monitored. The entire data are transferred to the internal PDA system and filed.
Thanks to easily replaceable and coded installation kits a rapid change to other types is possible which makes this concept highly flexible.
Services provided by VESCON:
- concept development
- development and construction of several turnkey plants
- training courses
- production support
- maintenance and servicing
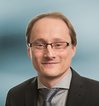
VESCON provides motion: Assembly line with EOL test bench for VW rear axles of the VW Caddy 4motion.
Task: | assembly line with EOL test bench | |
Department: | special machinery engineering | automation | |
Business: | automobile industry |
Within a period of 27 weeks - from order to delivery - VESCON has developed a turnkey assembly line for rear axles for the VW or MAGNA engineering centre in St. Valentin. The challenge was to guarantee a high flexibility allowing the personnel to take strong influence on the process when handling different production quantities on the one hand, and to ensure the same process safety and measuring system capability as with fully automated lines on the other hand.
The plant has been designed in such a way that a worker can either "walk along with" the axle through the production process, or - in case of a higher production volume - pass the workpiece carrier on to the next worker. Depending on the customers' call-offs one up to 6 workers can operate the plant.
This required the development of a PLC higher-level production data acquisition solution (PDA) including an interface to the internal SAP system. In the PDA system all process parameters, results and personnel data are recorded.
In the first plant section the raw, painted rear axle as well as bevel gears and crown wheel are measured via an integrated Zeiss measuring machine. Then follow the assembly of the gearbox and the backlash and friction measurements as well as the assembly of the half-axles and the wheel hubs with brake discs. After this the Haldex clutch is fitted. Of course, torques and rotation angles in the screwing processes and pressing forces and ways in the pressing processes are recorded and controlled as well. The quality-relevant processes like measuring, pressing and screwing as well as the test run take place in a fully automated way. By indication via the PLC unit the worker is guided through the workflow and has to confirm the completion of the individual worksteps.
The finished rear axle is filled with two different oils on the EOL test bench before it has to undergo the test run (Haldex, gearbox, ABS sensor system).
During an iO run the axle is finally embossed and the corresponding assembly and test records are created. By this procedure it is guaranteed that the driven rear axles in the VW Caddy 4motion run smoothly and to the customer's satisfaction.
Services provided by VESCON:
- concept development
- development and construction of a turnkey plant
- process data acquisition (PDA) with SAP interfaces
- training courses
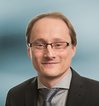
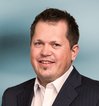
Division Head Software Development
Phone +43 3112 36006-400
martin.feichtgraber@vescon.com